How PackRyt Diverter Improves Shaft Sealing in the Paper Industry
In the paper industry, there are two things that can have a massive negative impact on your operational efficiency and the longevity of your rotating shaft equipment:
- Not managing your flush water properly
- A bent deflected, or sagging shaft
Why? Because when flush water isn’t properly managed, it can lead to blockages. Meanwhile, a compromised shaft can cause regular leaks when the seal breaks from repeated use fails from shaft movement.
SealRyt’s PackRyt® Diverter addresses these needs by simplifying the sealing process, improving flush water management, and enhancing shaft reliability.
This leads to smoother operations, fewer disruptions, and increased production rates, making it a valuable solution for the paper industry.
The Challenge with Traditional Sealing Methods for Pumps and Shafts in Paper Production
Traditional stuffing box sealing methods for pumps in the paper industry often use outdated lantern ring/packing stuffing box configurations. These systems typically place the flush water port at the bottom of the stuffing box, leading to several problems:
● Excessive Flush Water: High volumes of flush water flow directly into the process, which can contaminate the paper pulp and cause inefficiencies.
● Increased Wear and Tear: Excessive flush volumes can introduce slurry into the stuffing box, accelerating wear on expensive components and increasing maintenance costs.
● Manual Adjustments: Manual adjustments to flush flow can be inconsistent, allowing solids to enter and damage parts.
The PackRyt Diverter Solution
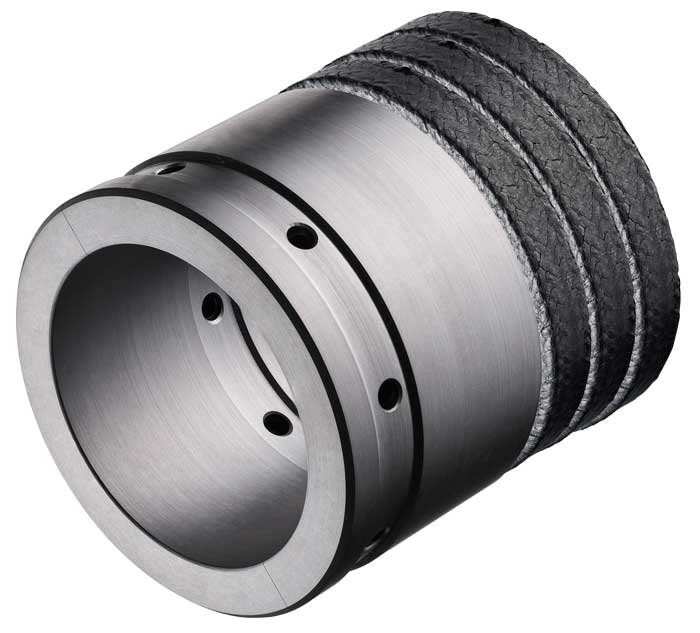
The PackRyt® Diverter is a stuffing box sealing arrangement that includes a flush channel relocation system within the composite bearing. It replaces outdated lantern ring/packing configurations and offers several benefits.
Flush Relocation Without Equipment Modification
● Optimized Flush Volume Management: The Diverter relocates the flush channel to a position suited for paper production, reducing flush volume by up to 85%. This prevents excess water from contaminating the paper pulp and minimizes process disruptions.
● Increased Shaft Concentricity: The Diverter, which acts as a bearing, maintains shaft concentricity, enhancing sealing reliability and extending equipment life in paper mills.
Key Advantages of the Diverter
● Machined to close-clearance, the bearing stabilizes the shaft and prevents movement
● Cavitation caused deflection is minimized.
● Results in minimal friction to the sleeve/shaft.
● Minimal clearance sharply throttles solids, which allows the low-flush to keep them out of the shaft area.
● Flush use reduction could be up to 865%.
● Flush flow remains constant.
● Automatically positions the flush channel correctly so the lantern ring cannot move past flush inlet.
● Little, or in some cases, no leakage from gland follower to atmosphere.
● Eliminates the need to constantly adjust packing.
● As few as two rings of packing are required.
● High-performance, ultra-pure heat conductive sealing rings can virtually eliminate sleeve/shaft wear.
See the PackRyt Diverter in Action
Watch our video titled “A Dilution Pump with a SealRyt Diverter System - Before and After” to see the PackRyt Diverter in action as it’s used to seal a problematic dilution pump at a paper mill in Texas.
Why Choose SealRyt’s PackRyt Diverter?
The PackRyt® Diverter addresses the inefficiencies of traditional sealing methods in the paper industry and offers improvements in performance and reliability. Integrating this advanced sealing system can lead to significant operational enhancements and reduced maintenance costs.
For more information, visit the PackRyt® Diverter product page.
If you want to learn more about pump seals, mechanical packing, failure points, or any rotating shaft sealing questions then contact one of our engineers. We have been sealing shafts for over 20 years in all types of industries.