Shaft Sealing - BLR Bearing with Lantern Ring
The PackRyt® Sealing System is a unique stuffing box sealing arrangement that incorporates a bearing and flush channel system together. This replaces outdated packing/lantern ring/packing configurations. It can also replace hard-to-maintain mechanical seals. Our system brings shafts into concentricity and keeps them there, significantly increasing sealing reliability.
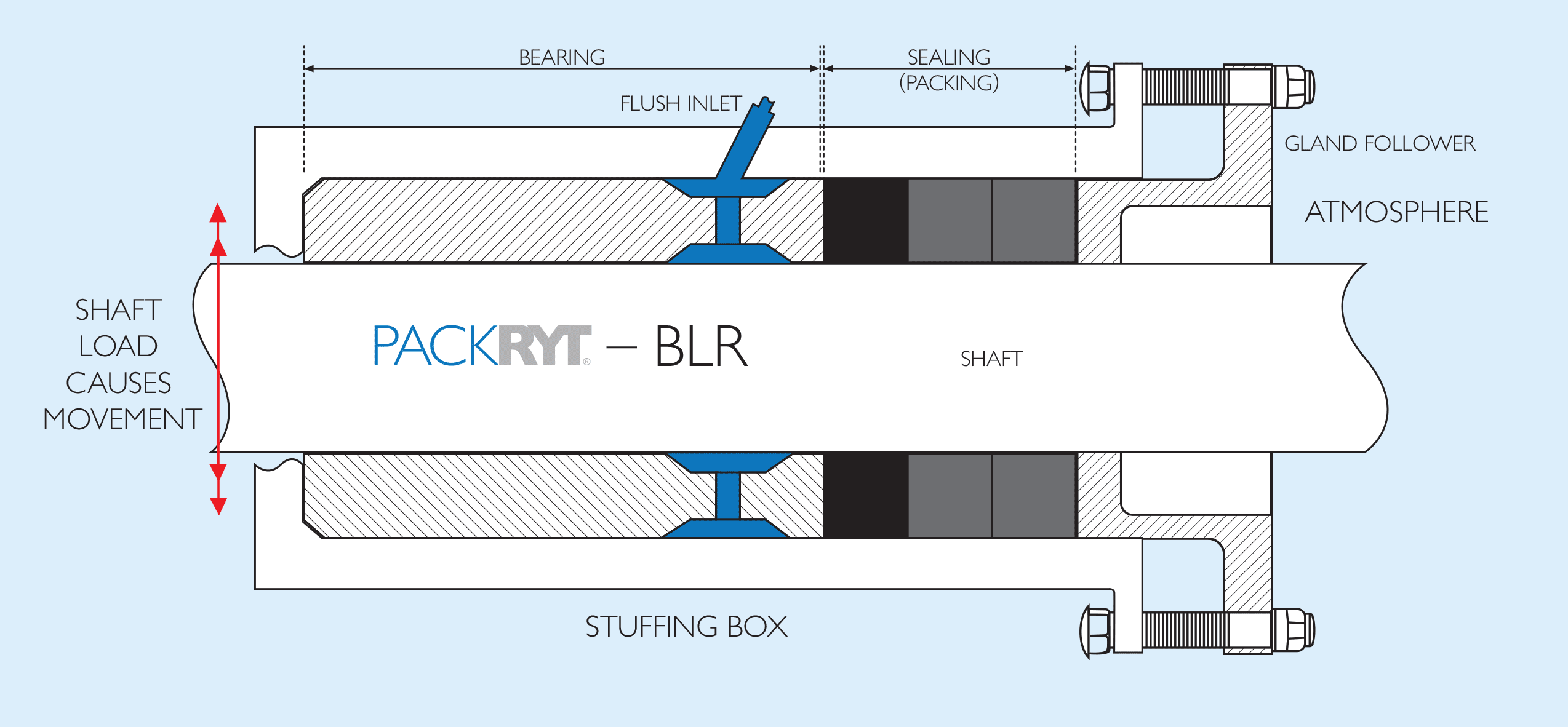
Don't be fooled by copy-cats with inferior designs and materials.
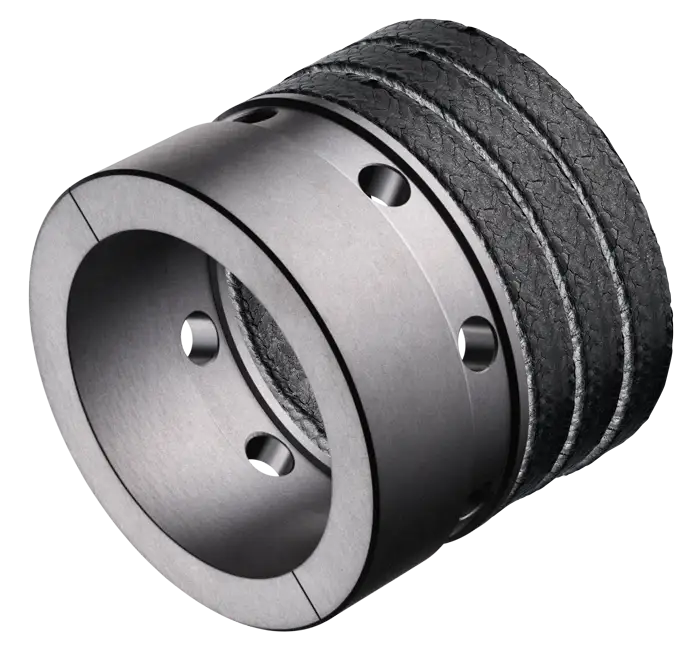